A Brief Review of Methods and Requirements
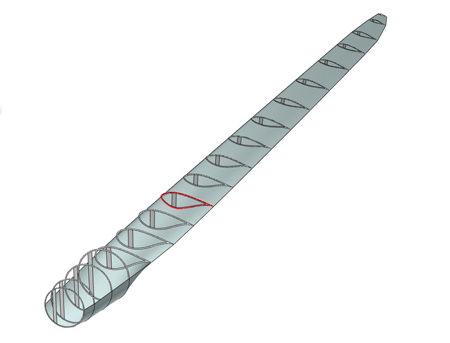
By Joseph Youssif Saab Jr and Alexandre Martuscelli Faria, Brazil
Windtech International wants to make your visit to our website as pleasant as possible. That is why we place cookies on your computer that remember your preferences. With anonymous information about your site use you also help us to improve the website. Of course we will ask for your permission first. Click Accept to use all functions of the Windtech International website.