New Poul la Cour Tunnel at DTU Risø
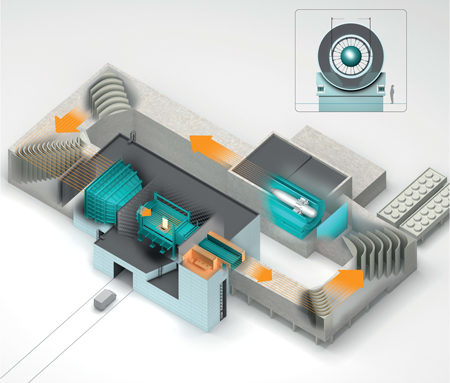
By Nicholas Gaudern, Chief Technical Officer, Power Curve, Denmark
Windtech International wants to make your visit to our website as pleasant as possible. That is why we place cookies on your computer that remember your preferences. With anonymous information about your site use you also help us to improve the website. Of course we will ask for your permission first. Click Accept to use all functions of the Windtech International website.